怪我人が止まらない?その原因、ローテーション不足かも
今日の申し送り
作業のローテーションなしは、まるで「壊れるまで使う機械」と同じだ。人間の体にも限界がある!
「また一人、腰を痛めて退職か…」
工場の現場リーダーなら、一度はこんな状況に直面したことがあるはずだ。長年の経験者が突然戦線離脱し、人員不足がさらに深刻化。その穴埋めをするために、残った作業員にさらに負担がかかる…負の連鎖が続く。
「労災対策はしてるし、安全ルールも守らせている。でも怪我人は減らない。なぜだ?」
そう考えたことはないだろうか?
実はその根本的な原因、作業ローテーションがないことかもしれない。
単一作業を長期間続けることで、身体の特定部位に負荷が集中し、慢性的な痛みや障害を引き起こす。「慣れた作業だから効率がいい」という考えが、逆に怪我人を増やす元凶になっているのだ。
本記事では、ローテーション不足がなぜ問題なのかを深掘りし、解決策を探っていく。
同じ作業を続けることの「見えないリスク」
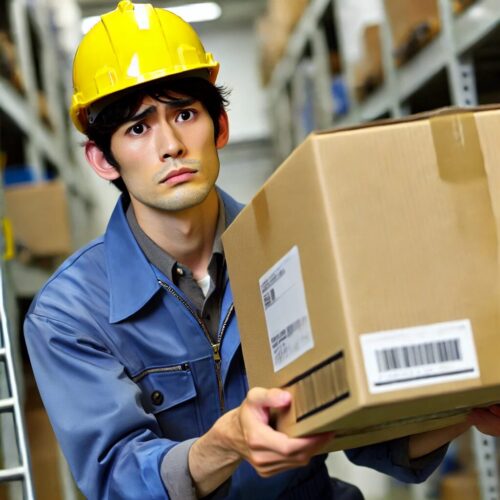
■ 工場現場で多発する「慢性的な怪我」
単一作業を長時間続けることで、どんな影響があるのか?
現場では、以下のような怪我や体調不良が頻発している。
- 腰痛・関節痛(重量物の持ち上げ作業、立ち作業の継続)
- 腱鞘炎・腕のしびれ(繰り返し動作による神経圧迫)
- 頸椎・肩の障害(長時間の不自然な姿勢の維持)
「最初は少し痛いくらいで、我慢できると思ってた。でも気づいたときにはもう仕事が続けられない状態になってた」
こうした声は、現場を離れた作業員たちからよく聞かれる。つまり、単一作業を長期間続けることは、身体に“見えないダメージ”を蓄積させるのだ。
私も被害者の一人
わたしの経験として、3年間同じプレス作業を続けた結果、肩を慢性的に痛めてしまったという現実がある。
これは、単一作業の長期継続によって、特定の部位に負荷が集中し、回復する時間がないままダメージが蓄積されてしまった典型的な例だ。
✅ 最初は軽い違和感だったが、時間が経つにつれて痛みが慢性化
✅ 湿布やストレッチでは改善せず、作業を続けるほど悪化
✅ ローテーションがなかったため、回避できる選択肢がなかった
この経験から、ローテーションがないことで作業者の健康に深刻な影響を及ぼすことを身をもって理解した。
もし、適切なタイミングでローテーションが導入されていれば、負荷の分散ができ、肩を痛めることなく仕事を続けられた可能性が高い。
このような現場のリアルな問題を解決するために、ローテーションの導入が必要不可欠であることを本記事では伝えていく。私と同じような経験をする人が減るよう、現場のリーダーが行動を起こすきっかけになればと思う。
■ さらに悪化する「人手不足の悪循環」
怪我や体調不良による離職が増えれば、その穴埋めのために他の作業員に負担がかかる。その結果、さらに疲労がたまり、新たな怪我人を生む…これが続くと、どんなに新しい人を雇っても、すぐに辞めてしまう。
「うちの工場は、いつも人が足りない」
そんな現場では、慢性的な怪我のリスクが蔓延している可能性が高い。現場リーダーとしては、「なんとか踏みとどまってほしい」と願うものの、実際には人が定着しない。ローテーションがない限り、同じ問題が繰り返されるのだ。
「ローテーション不足」と怪我の関係性
この問題は、決して珍しいことではない。実際に、国内外の研究やデータでも、**「単一作業の継続は身体に深刻なダメージを与える」**ことが指摘されている。
① 厚生労働省の労災データ
厚生労働省の統計によると、製造業における労災の約60%が、反復動作や不自然な姿勢の継続によるものとされている。特に、腰痛や腱鞘炎などの障害は、労災補償の対象になるほど深刻な問題だ。
② 海外の労働科学研究
アメリカ国立労働安全衛生研究所(NIOSH)の報告によると、単一作業を長期間続けると、関節や筋肉の慢性的な負担が原因で「職業性筋骨格系疾患(MSDs)」のリスクが3倍以上に跳ね上がるとされている。
この報告では、特に「単純な動作の繰り返しは、同じ部位の筋肉に極端な負担をかけるため、短期間で障害が発生しやすい」と警鐘を鳴らしている。
③ 企業の取り組み事例
実際に、ローテーションを導入した企業では、労災発生率が大幅に低下した事例もある。たとえば、ある自動車部品工場では、作業者のローテーションを2時間ごとに変更する制度を導入した結果、年間の労災件数が50%以上減少したというデータがある。
前編まとめ:怪我のリスクを防ぐには?
ここまで見てきたように、怪我人が続出する原因は単一作業の長期継続による身体の負担にある。そして、これを防ぐためには「作業ローテーションの導入」が不可欠だ。
だが、実際の現場では、
✅ 「うちの工場は忙しくてローテーションなんかできない」
✅ 「他の工程の教育を進める余裕がない」
✅ 「一度慣れた作業を変えると生産効率が落ちる」
といった理由で、ローテーションを敬遠している工場が多い。
特に、中小工場や下請け、子会社ではローテーションの重要性を軽視する傾向がある。反対に、大手工場では積極的にポジションローテーションを取り入れ、労災リスクを低減しながら生産性を向上させている。
この違いはどこから生まれるのか?
なぜ中小工場ではローテーションが進まないのか?
中編では、**「ローテーションが導入できない理由」**を掘り下げ、その背景にある教育システムや作業の仕組みの問題を分析する。
なぜ中小工場はローテーションを導入できないのか?
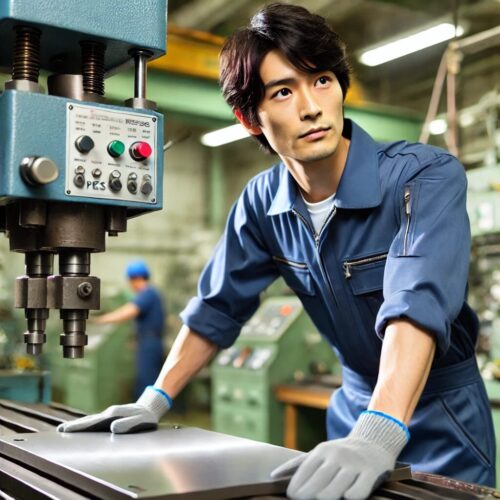
なぜローテーションが軽視されるのか?
■ 中小工場・下請け・子会社の現実
あなたの工場では、ローテーションを導入しようとしても、こんな言葉が飛び交っていないだろうか?
- 「今の作業員でなんとか回ってるから、変える必要はない」
- 「他の工程まで教育している時間がない」
- 「一人ひとりの役割が固定されてるから、ローテーションすると混乱する」
この考え方こそが、現場の怪我人を増やす元凶だ。
実際、**ローテーションが進まない理由は「人材の問題」ではなく、「工場の仕組みの問題」**にある。
特に、中小工場や下請け、子会社では、以下のような要因がローテーション導入を妨げている。
① 教育システムが整備されていない
大手工場では、新人が入ると段階的な研修があり、**多能工(マルチスキル)の育成が進んでいる。しかし、中小工場では、「まずは目の前の作業を覚えろ」**という文化が根強く、ローテーションの前に教育自体が不十分になりがちだ。
結果的に、**「あの工程は○○さんしかできない」**という属人化が発生し、特定の作業者に負荷が集中する。
② 短期的な生産効率しか見ていない
ローテーションを導入すると、一時的に生産効率が落ちる可能性がある。しかし、それを嫌って、目先の効率だけを重視し、長期的なリスク(怪我や離職)を軽視する経営層も多い。
大手工場では、「教育を施したうえでのローテーション」が長期的に見てコスト削減につながると理解しているが、中小工場では「余計な手間がかかる」と考えられてしまうのだ。
③ 作業が「標準化」されていない
ローテーションを行うには、各工程の作業内容が一定の基準でマニュアル化されている必要がある。しかし、多くの中小工場では、**「この作業はこの人のやり方」「ベテランの感覚でやる」**といった属人的な手法が多く、教育しづらい状態になっている。
つまり、「ローテーションができない」のではなく、「ローテーションしづらい環境を自ら作ってしまっている」可能性が高いのだ。
具体的な課題分析:なぜ大手工場はローテーションを進められるのか?
では、なぜ大手工場ではポジションローテーションが進んでいるのか? その違いを具体的に見ていこう。
① 教育システムが体系化されている
大手工場では、以下のような仕組みが整っている。
- 新人研修で複数の工程を学ぶカリキュラムがある
- 作業の標準マニュアルがあり、だれでも同じ品質で作業できる仕組みがある
- OJT(On-the-Job Training)が確立されている
このような教育システムがあるからこそ、ローテーションがスムーズに進む。
② 「多能工化」が生産性向上につながると理解している
たとえば、トヨタ自動車では、作業員を多能工化することで、生産ラインの柔軟性を向上させている。
- Aラインの人員が不足しても、Bラインから応援できる
- 特定の工程に依存しないため、トラブル発生時にも生産が止まりにくい
これは、長期的な視点で見れば、「一時的に教育に時間をかける」ことが、結果的に効率化につながるということを意味する。
③ 作業が標準化されている
大手工場では、どの作業者でも一定の品質を保てるように、作業手順が徹底的にマニュアル化されている。
- 「この工程は、この順番で、こういう手順で進める」
- 「この作業には、この工具を使う」
このように、すべての工程が「属人化しない仕組み」になっているからこそ、ローテーションが可能になる。
教育システムと作業の仕組みを整えれば、ローテーションは可能になる
ここまで見てきたように、**ローテーションが進まない工場は、「できない」のではなく、「やろうとする環境が整っていない」**だけだ。
では、どうすれば中小工場や下請け企業でも、ローテーションを導入できるのか?
次の後編では、以下の解決策を掘り下げる。
- ローテーションを可能にする教育システムの作り方
- どんな教育ステップを踏めば、無理なく他工程のスキルを習得できるのか?
- 「忙しいからできない」を解決する作業の仕組み作り
- マニュアル化・標準化を進めることで、現場が混乱せずにローテーションを導入する方法
- 実際にローテーションを導入した工場の事例
- ある中小工場がローテーションを成功させたケースを紹介
このまま「同じ作業を続けさせる現場」にするのか、それとも「ローテーションで働きやすい現場」にするのか?
次の後編で、現場リーダーが今すぐ実践できる解決策を紹介する。
ローテーション導入で怪我人ゼロへ!実践できる解決策と成功事例
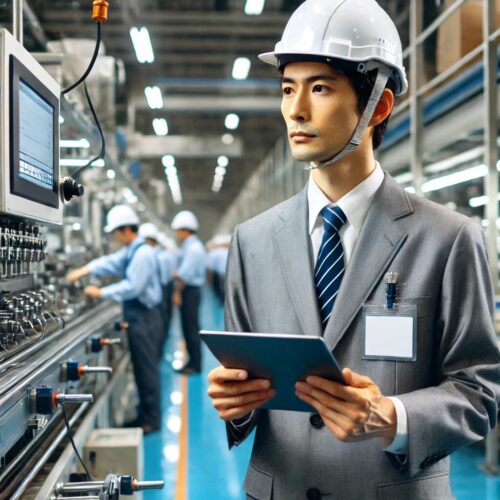
「忙しいからできない」を解決する作業の仕組み作り
ローテーションを実現するには、教育体制の見直しだけでなく、作業の仕組み自体を整えることが重要だ。
「教育に時間を取れない」「生産性が落ちる」という声が上がるのは、ローテーションのための準備ができていないからだ。作業を標準化し、スムーズにローテーションできる環境を整えることで、現場の負担を最小限に抑えながら導入できる。
以下の具体策を順番に進めていこう。
1. マニュアル化・チェックリストの導入
「作業ごとにやり方が違う」ではローテーションが回らない。標準化されたマニュアルが必要!
ローテーションを導入しようとしても、作業者ごとにやり方が違う、経験者しか分からない作業が多い状態では、教育に時間がかかりすぎる。これを防ぐために、まずは作業をマニュアル化し、誰がやっても同じ品質で作業ができる状態を作ることが重要だ。
✅ 作業の標準マニュアルを作る
- 文章だけでなく、写真・イラスト・動画を活用し、初心者でも分かる内容にする
- **「こうするべき」ではなく、「こうすれば誰でもできる」**という視点で作成する
- **ベテラン作業者の技術を形式知化(マニュアル化)**し、属人化を防ぐ
✅ チェックリストで作業の精度を上げる
- 作業工程ごとにチェックリストを作成し、ミスを防ぐ
- ローテーション時の「引き継ぎ事項」も明記しておき、作業のバラつきを減らす
📌 成功事例:トヨタの「カイゼン方式」 トヨタ自動車では、すべての作業をマニュアル化し、標準作業を徹底することで多能工化を成功させた。これにより、新しい作業者が短期間で戦力化でき、ローテーションがスムーズに進む仕組みができている。
2. 工程ごとの「スキルマップ」を作る
「誰が何の作業をできるか分からない」ではローテーションが機能しない。可視化がカギ!
ローテーションを円滑に進めるには、誰がどの工程をどのレベルでこなせるのかを一目で分かるようにすることが重要だ。これを実現するのが「スキルマップ」だ。
✅ スキルマップの作成
- 縦軸に作業者名、横軸に工程をリストアップし、各作業者の習熟度を「〇」「△」「×」で表示
- 習熟度ごとにランクをつけ、「△→〇」にするための教育計画を立てる
✅ 活用方法
- 不足しているスキルを特定し、教育計画を明確にする
- 「この人が抜けても、この人が対応できる」というローテーション計画を立てやすくする
- 人員配置を柔軟にし、特定の作業者に負担が偏らないようにする
📌 成功事例:名北工業のスキルマップ導入 名北工業株式会社では、スキルマップを活用し、各作業員の習熟度を可視化。
これにより、ローテーションを組みやすくなり、多能工化がスムーズに進行。生産性向上と労災リスクの低減に成功した。
▶ 情報提供元:protrude.com
3. 短時間ローテーションを試す
「最初から長時間のローテーションを導入しない。小さく始めて、現場の抵抗をなくす!」
「ローテーションを入れると、生産効率が落ちるのでは?」と不安に思う現場も多い。
そこで、まずは短時間ローテーションを試し、負担を最小限に抑えながら導入する方法を取る。
✅ 最初は「2時間ごとのローテーション」など、短いスパンで試す
- 1日のうち、2時間だけローテーションを実施し、作業者の負担を確認する
- 週に1回だけローテーション日を設けるなど、現場の混乱を防ぎながら進める
✅ 小規模なテスト運用から始め、現場のフィードバックを取りながら改善
- 作業者の意見を聞きながら、無理のない範囲でローテーションを広げていく
- 「負担が大きい」と感じた部分を改善しながら、徐々にローテーションの時間を伸ばしていく
📌 成功事例:トヨタの「短時間ローテーション」 トヨタでは、多能工化を進める際に、いきなり全工程を担当させるのではなく、まずは短時間のローテーションからスタート。徐々にスキルを習得させることで、無理なく生産性向上につなげている。
▶ 情報提供元:hancho.jp
まとめ:ローテーションは「忙しいから無理」ではなく、「仕組みを整えればできる」
ローテーション導入が進まない理由として、「教育に時間を取れない」「忙しくてできない」「生産性が落ちる」という意見があるが、それはローテーションのための準備ができていないだけだ。
以下の3つのアクションを実行すれば、ローテーションはスムーズに進められる。
✅ 作業の標準化(マニュアル・チェックリストの作成)
✅ スキルマップで習熟度を可視化し、計画的に多能工を育てる
✅ 短時間ローテーションから始めて、徐々に負担を減らしながら進める
「忙しくてできない」ではなく、「どうすればできるか?」を考え、少しずつ現場を改善していくことが重要だ。
ローテーションを導入することで、
✅ 怪我人が減る
✅ 生産性が向上する
✅ 離職率が改善する
✅ 現場が柔軟に対応できるようになる
現場リーダーであるあなたが、まず一歩を踏み出すことで、職場環境は確実に変わる!
記事の総まとめ】ローテーション導入で怪我人ゼロ&生産性向上!
工場で怪我人が続出する大きな原因は、単一作業の長期継続による身体の負担だった。特に中小工場や下請け企業では、ローテーションの重要性が軽視され、特定の作業者に負荷が集中している現実がある。
しかし、ローテーションを導入すれば、
✅ 怪我人の減少
✅ 作業者の負担軽減
✅ 生産性の向上
✅ 離職率の低下
✅ 現場の柔軟な対応力アップ
といったメリットを得られる。
ローテーション導入の成功ポイントは3つ!
- 教育システムを整え、段階的に多能工化を進める
- 作業の標準化とスキルマップの活用で、誰でも一定の品質で作業できる環境を作る
- 短時間ローテーションから始め、現場の負担を最小限にしながら導入する
実際に成功した企業の事例(トヨタ、名北工業など)でも、多能工化を推進することで、生産性向上と労災リスクの低減を実現している。
「忙しくてできない」「教育の時間がない」は言い訳だ。仕組みを整えれば、どんな現場でもローテーションは可能!
今こそリーダーであるあなたが一歩を踏み出し、現場を変えていこう!