今日の申し送り
日本の製造業は、時代遅れの設備とマンパワーに頼った生産体制を続けている。このままでは競争力を失い、国際市場から取り残される未来が待っている。
「日本の製造業はすごい」「品質が高い」と言われていたのは、もう過去の話かもしれない。
現場に足を踏み入れれば、今でも30年前の機械が現役で動いている工場がザラにある。
老朽化した設備をメンテナンスでなんとか延命し、壊れたら人手でカバーする──そんなやり方が、いつまでも通用するはずがない。
実際、海外のメーカーが日本の工場を視察したとき、「こんな非効率なことを、うちの従業員にはさせられない」と言い捨てて帰ったという話もある。
そして、これは決して一部の話ではない。
大手の製造メーカーも同様に平然と時代遅れの設備を主力設備として運用している。
俺自身、かつて勤めていた工場で、海外からの視察団に「これは博物館か?」と笑われた経験がある。彼らにしてみれば、半世紀前の設備を使い続け、最新の技術を導入しようとしない日本の工場は、もはや「化石」のように見えたのだろう。
なぜ日本の製造業は、こんなにも古い設備にしがみついているのか? その結果、どんな問題が起きているのか?
データで見る日本製造業の「化石化」
では、この「化石設備」の問題、日本全体でどれほど深刻なのか?
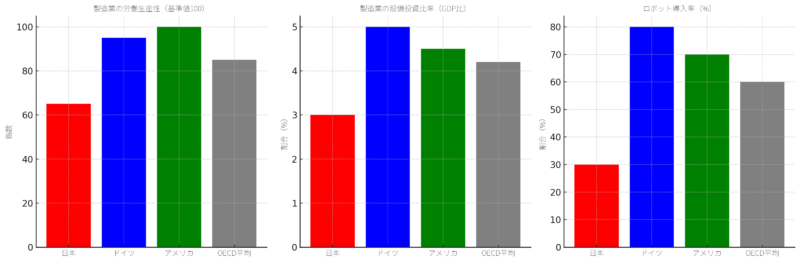
【データ1】設備投資の低迷
解説: 設備投資 とは、工場の機械や技術を新しくするためにお金を使うこと。これが増えれば、生産性が向上し、国際競争力が高まる。
データ:
日本の製造業の設備投資額は ここ20年間ほぼ横ばい。
海外の先進国はAIやIoT活用のための設備投資が増加 している。
- 日本の製造業の設備投資比率(GDP比):約 3%(20年間ほぼ変わらず)
- ドイツの製造業の設備投資比率(GDP比):約 5%(継続的に増加)
- アメリカの製造業の設備投資比率(GDP比):約 4.5%(年々増加)
【データ2】ロボット導入率の低さ
解説: ロボット導入率 とは、工場でロボットをどれだけ活用しているかを示す指標。高いほど、自動化が進んでいる。
データ:
日本は かつて「ロボット大国」 と言われていたが、今ではその座を失いつつある。
特に中小企業では、ロボットや自動化設備の導入が遅れている。
- ドイツの製造業におけるロボット導入率:80%以上
- アメリカの製造業におけるロボット導入率:70%以上
- 日本の中小製造業におけるロボット導入率:30%以下
【データ3】労働生産性の低迷
解説: 労働生産性 とは、「1人あたりの労働者が、どれだけの価値を生み出しているか」を示す指標。数字が高いほど効率的。
データ:
OECD(経済協力開発機構)のデータによると、日本の労働生産性は先進国の中でも最下位クラス。
特に製造業の労働生産性は、ドイツやアメリカの約2/3程度しかない。
- アメリカの製造業の労働生産性(GDP換算):約 100(基準値)
- ドイツの製造業の労働生産性(GDP換算):約 95
- 日本の製造業の労働生産性(GDP換算):約 65
出典: OECD 労働生産性統計
これらのデータから、日本の製造業は 「設備投資が停滞」「ロボット導入が遅れ」「労働生産性が低い」 という深刻な問題を抱えていることが明確だといえる。
古い設備にしがみつくことのデメリット
古い設備を使い続けることには、いくつかの重大なデメリットがある。
1. イノベーションの遅れ
最新の設備を導入しないということは、競争力のある新しい技術を使えないということ。
例えば、ドイツの「インダストリー4.0」や、アメリカの「スマートファクトリー」では、AIやIoTを活用して生産効率を劇的に向上させている。
一方、日本はどうだ?
- ・手作業でデータを記録
- ・紙の帳票を使って工程管理
- ・未だに「ベテランの勘」に頼る品質管理
こんな状態で、世界と戦えるわけがない。
2. マンパワーへの過剰依存
日本の製造業は、現場の作業員の技能に頼りすぎている。
熟練工が一人辞めるだけで生産性が落ちるなんて、今の時代にありえない話だ。
実際、大手自動車メーカーの生産ラインを視察した海外のメーカーが、「こんな非効率な作業を、うちの従業員には絶対にやらせない」と言った話がある。
海外では、人がやらなくてもいい作業は自動化するのが当たり前なのだ。
それなのに、日本では「人間のほうが臨機応変に対応できる」といまだに信じられている。
だが、その「臨機応変」は、本当に必要なのか?
最新の自動化技術を導入すれば、そもそも「臨機応変に対応する必要がない」状態を作れるはずだ。
3. 老朽化によるリスク
設備が古くなれば、当然、故障のリスクも増える。
そして、部品が手に入らなくなれば、修理もできなくなる。
俺のいた工場でも、「この機械が壊れたら、もう替えがないから終わりだな」と冗談半分に言っていた設備が、実際に壊れて生産停止したことがある。
しかも、その復旧には何日もかかる。
「とりあえず動いているから」と古い設備を使い続けた結果、いざトラブルが起きると、どうにもならなくなるのだ。
こうしたリスクを放置し続けているのが、今の日本の製造業の現状だ。
■ まとめ:古い設備を使い続けるのは「悪習」
- ・日本の製造業は、老朽化した設備にしがみついている
- ・その結果、イノベーションの遅れ、マンパワー依存、老朽化によるリスクが発生
- ・海外と比較すると、日本の設備投資もロボット導入率も低すぎる
では、この問題をどう解決すべきなのか?
中編では、なぜ日本の製造業が「化石化」してしまったのか、その背景を掘り下げる。
なぜ日本の製造業は「化石化」してしまったのか?
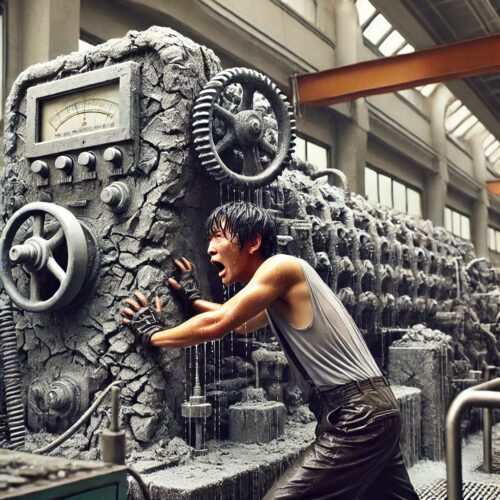
日本の製造業が古い設備を使い続けるのには、それなりの理由がある。だが、その理由こそが、日本の競争力を削ぎ落としている要因だ。このままでは、世界から取り残される未来が確定してしまう。
なぜ日本の工場は古い設備を捨てられないのか?
古い設備を使い続けるのは、単なる「ケチ」や「怠慢」だけではない。そこには、日本特有の経済的・文化的な背景が絡んでいる。
1. 「減価償却が終わるまで使い続ける」文化
日本企業は、設備投資をする際に減価償却期間を重視する傾向が強い。
例えば、新しい機械を導入した場合、会計上は数年にわたって減価償却しなければならない。つまり、投資したコストを回収するまでは「使い倒さないと損」と考えるわけだ。
・欧米企業:「新しい技術が出たら、償却期間に関係なく投資」
・日本企業:「償却期間が終わるまで、壊れるまで使い続ける」
結果、日本では「30年前の設備が現役」という状況が生まれる。最新の技術が登場しても、「まだ使えるから」という理由で見送られるのだ。
2. 設備投資を渋る企業文化
日本の製造業は、バブル崩壊以降、コストカットを優先する経営が続いている。
特に中小企業では「とりあえず今ある設備でなんとかする」という意識が根強い。
・「新しい機械を買うより、修理したほうが安い」
・「設備投資のための予算がない」
・「導入しても現場のオペレーターが使いこなせない」
こうした理由で、最新の設備投資が後回しにされるのだ。
特に、現場の人間が「今のやり方で十分」と思っていると、経営層も投資に踏み切れない。
3. 人間の技術を重視しすぎる風潮
日本は「職人技」にこだわる文化が強い。
そのため、自動化よりも「熟練工の技」を重視する傾向がある。
・「職人の勘と経験が品質を支えている」
・「機械ではできない細かい調整が必要」
・「人間の方が臨機応変に対応できる」
確かに、職人の技術は素晴らしいものだ。
しかし、ドイツやアメリカでは、その「技術」すらデジタル化して、AIに学習させる動きが進んでいる。
人間の手に頼りすぎた結果、労働力不足になったときに対応できなくなるのが、日本の製造業の弱点だ。
日本の製造業が抱える「化石化」の問題
1. 「ブラックボックス化」した技術
古い設備を使い続けると、そこには「属人化」の問題が発生する。
たとえば、「この機械の調整は〇〇さんしかできない」という状況が起こりがちだ。
- ・熟練工が辞めると、設備の運用方法が分からなくなる
- ・マニュアルがないため、新人が育たない
- ・結果として、ますます人に頼る構造になる
ドイツでは、こうした問題を防ぐために、生産プロセスをデータ化し、誰でも作業できる環境を整えている。
一方、日本では「勘と経験」に頼るため、新しい人材が育たない。
2. 最新技術への適応の遅れ
海外の製造業では、AIやIoTを活用した「スマートファクトリー化」が進んでいる。
しかし、日本では導入が遅れ、「昔ながらのやり方」を続けている企業が多い。
- ・IoTを導入している日本の中小企業:30%以下
- ・AIを活用した品質管理を行っている企業:20%以下
これでは、海外勢に太刀打ちできるはずがない。
出典:日本のAI(人工知能)導入状況と導入の必要性、業界別の活用事例を解説
3. 「とりあえず修理すればいい」精神
設備が壊れても、新しいものに買い替えるのではなく、「とりあえず直して使う」という考え方が根強い。
- ・「補修部品がないから、中古市場で探す」
- ・「メーカーがサポートを終了した機械を、社内でなんとか修理」
- ・「古い設備のために、専用の職人が必要になる」
これにより、設備の稼働率が低下し、長期的には生産性が下がる。
■ 海外との比較:どれだけ差がついているのか?
1. ドイツの「インダストリー4.0」
ドイツでは、国家レベルで製造業のデジタル化を推進している。
工場内の設備はすべてネットワークでつながり、AIが最適な生産計画を自動で立案する。
- ・AIが異常を検知し、メンテナンスを事前に実施
- ・作業員がいなくても、自律的に生産が進む
- ・クラウドを活用し、リアルタイムでデータを分析
結果として、労働生産性は日本の約1.5倍に達している。
2. アメリカの「スマートファクトリー」
アメリカでは、最新のロボット技術を積極的に導入し、「人手のいらない工場」を目指している。
- ・生産ラインの9割以上がロボット化
- ・データ分析を活用し、リアルタイムで生産効率を最適化
- ・熟練工の技術をAIに学習させ、人に依存しないシステムを構築
この結果、人件費が高いアメリカでも、競争力を維持できている。
■ まとめ:なぜ日本は「化石」になったのか?
- ・減価償却を重視するあまり、新技術の導入が遅れる
- ・コスト削減を優先し、設備投資が後回しにされる
- ・熟練工に頼りすぎて、自動化が進まない
- ・ブラックボックス化した技術が、新人育成の障害になっている
こうした要因が絡み合い、日本の製造業は「化石化」してしまった。
では、どうすればこの状況を打破できるのか?
後編では、具体的な解決策を提案し、実際の企業事例を紹介する。
化石設備からの脱却──日本の製造業が生き残るための改革案
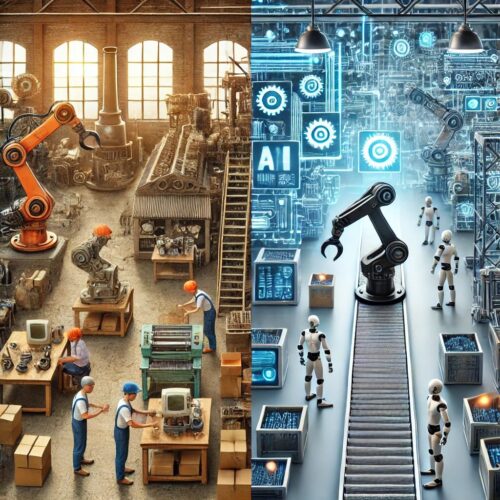
古い設備にしがみついた結果、日本の製造業は競争力を失いつつある。だが、まだ手遅れではない。設備更新とデジタル化、そして意識改革ができれば、日本の工場は再び世界のトップに返り咲くことが可能だ。
日本の製造業が今すぐやるべきこと
日本の製造業が「化石化」から脱却するには、次の3つのステップが必要だ。
- 「減価償却優先」思考からの脱却──設備更新の意識改革
- デジタル化・自動化の徹底導入
- 海外企業に学ぶ「スマートファクトリー化」戦略
1. 「減価償却優先」思考からの脱却──設備更新の意識改革
まず、企業の経営層は「設備は償却期間が終わるまで使い続ける」という発想を捨てる必要がある。
欧米企業の考え方を見てみよう。
彼らは「投資した設備が競争力を生まなくなったら即座にリプレースする」という考え方が基本だ。
【アクションプラン】
✅ 設備投資のROI(投資対効果)を見直し、「古い設備を維持するコスト」と「新規投資のメリット」を正しく比較する。
✅ 減価償却が終わるまで待たず、競争力を維持するための「戦略的リプレースメント」を実施する。
✅ 国や自治体の設備投資補助金を積極的に活用する。
2. デジタル化・自動化の徹底導入
日本の製造業が「職人の技」にこだわりすぎるあまり、デジタル技術の導入が遅れているのは前編・中編で述べたとおり。
ここで重要なのは、**「デジタル化」と「自動化」は別物だが、セットで考える必要がある」**という点だ。
【具体的な施策】
✅ IoTの導入
・生産設備をネットワークに接続し、リアルタイムでデータ収集。
・AIを活用し、異常検知や予知保全を実施。
✅ AI・データ解析の活用
・熟練工の技術をデジタル化し、AIに学習させる。
・品質管理を「勘と経験」ではなく、データ分析で行う。
✅ ロボットの活用
・単純作業を自動化し、人手不足の解消。
・「人がやらなくていい仕事」を機械に任せ、作業者は監視やメンテナンスにシフト。
海外企業に学ぶ「スマートファクトリー化」戦略
日本の製造業が生き残るためには、海外の成功事例から学ぶことが不可欠だ。
ここでは、すでに「化石設備」から脱却し、競争力を取り戻した企業の実例を紹介する。
事例①:トヨタの「TPS×デジタル化」戦略
トヨタは長年、「トヨタ生産方式(TPS)」を掲げ、徹底的な効率化を追求してきた。
近年、このTPSにデジタル技術を融合させ、さらなる競争力向上を図っている。
具体的な取り組み
✅ AIとIoTによるリアルタイム生産管理
・各生産ラインのデータをAIが解析し、最適な生産スケジュールを自動生成。
✅ AGV(自動搬送ロボット)の導入
・部品供給をロボット化し、作業者の負担を軽減。
✅ 熟練工の技術をデジタル化
・「職人技」をVRやAIに学習させ、若手育成の効率を向上。
その結果、トヨタの生産性は大幅に向上し、「人力頼み」の生産ラインから脱却しつつある。
事例②:ドイツ・シーメンスの「デジタルツイン工場」
ドイツのシーメンスは、すべての工場を「デジタルツイン化」し、物理的な工場と同じ環境を仮想空間に作ることで、生産性を最大化している。『シーメンス(Siemens AG) は、ドイツを本拠とする 世界最大級の総合電機メーカー』
具体的な取り組み
✅ 仮想工場(デジタルツイン)の構築
・すべての生産設備を3Dデータ化し、シミュレーション可能に。
✅ AIによるリアルタイム最適化
・AIが生産スケジュールを管理し、材料や人員の配置を最適化。
✅ 完全な自動化生産ライン
・人が介在せず、ロボットが100%生産を担うラインの実現。
結果、シーメンスは生産効率を30%以上向上させ、低コストかつ高品質な製品を供給している。
事例③:アメリカ・テスラの完全自動化工場
テスラのギガファクトリーは、従来の自動車工場とは一線を画す存在だ。
「人の手を極力排除し、ロボットだけで製造する」ことを目標に、徹底した自動化が進められている。
具体的な取り組み
✅ 100%ロボット化された組立ライン
・従業員の手作業を最小限に抑え、生産速度を大幅に向上。
✅ AIによる品質管理
・カメラとセンサーが常時稼働し、不良品を即座に検出。
✅ サプライチェーンの完全デジタル化
・部品の発注から製造、出荷までをAIが一括管理。
この結果、テスラは1台の車を約10時間で生産することに成功している。
テスラの生産ラインのライオフ時間は約30秒であり、日本の自動車メーカーの60~90秒と比べて短く、生産効率が高いことが示されています。
後編のまとめ
✅ 古い設備を捨て、新しい技術に投資せよ
✅ 職人技に頼らず、デジタル技術を活用せよ
✅ 海外の成功事例から学び、スマートファクトリー化を進めよ
「このままではヤバい」と気づいたら、今すぐ動くべきだ。
変化を恐れず、新しい技術を取り入れなければ、日本の製造業は本当に「化石」と化してしまう。
日本の工場に未来はあるのか?
それは、今ここで「変わる」ことができるかどうかにかかっている。
記事全体のまとめ:化石設備にしがみつく日本の製造業、このままでは世界に取り残される!
日本の製造業は、古い設備を使い続けることで競争力を失いつつある。このままでは、世界市場から取り残される未来が待っている。
本記事では、「なぜ日本の製造業は化石化したのか」「海外との比較」「どのように改革すべきか」 を掘り下げた。
1. 日本の製造業が直面している3つの問題
① 設備投資の遅れ → 最新技術の導入不足
- 日本の製造業の**設備投資比率(GDP比)は約3%**で、ドイツ(5%)、アメリカ(4.5%)と比べて低い。
- 「減価償却が終わるまで使う」文化により、新しい技術が導入されにくい。
② マンパワー依存 → 自動化の遅れ
- 日本の中小製造業におけるロボット導入率は30%以下。
(ドイツ:80%以上、アメリカ:70%以上) - 「職人技」に頼る文化が根強く、自動化が進まない。
- 最新のAI・IoT技術の導入も遅れており、スマートファクトリー化が進んでいない。
③ 労働生産性の低迷 → 世界に取り残される
- 日本の製造業の労働生産性は、アメリカの約65%、ドイツの約68%と低い。
- テスラの工場では、1台の車を約10時間で生産 できるのに対し、日本の自動車メーカーでは16〜17時間かかる。
- 海外企業はデータ活用による効率化・最適化を徹底しているが、日本は「経験と勘」に頼りがち。
2. 日本が学ぶべき海外の成功事例
【シーメンス(ドイツ)】世界最先端のスマートファクトリー
- 工場全体をデジタルツイン(仮想空間でシミュレーション)化し、リアルタイムで生産効率を最適化。
- 生産の75%以上が完全自動化され、人の手をほとんど使わない。
【テスラ(アメリカ)】完全自動化された次世代工場
- 1台の車を約10時間で生産(日本の約1.5倍のスピード)。
- AI・ロボットを最大限活用し、「人手のいらない工場」を実現。
3. 日本の製造業が今すぐやるべきこと
✅ 設備投資を拡大し、最新技術を積極的に導入する
✅ IoT・AIを活用し、生産プロセスをデジタル化する
✅ ロボット導入を進め、単純作業を自動化する
✅ 「職人技」だけに頼らず、技能のデータ化を進める
■ 結論:このままでは日本の製造業は「化石」になる!
日本の製造業は、世界と戦うために、「古いやり方」から脱却し、最新技術を活用したスマートファクトリーへ進化する必要がある。
このままでは、いずれ**「日本の工場は時代遅れ」と海外から完全に見放される**可能性が高い。
「まだ使えるから」ではなく、「世界に勝つために何をすべきか」 を考え、今すぐ改革に乗り出すべきだ!