「ノーミスが当たり前」の職場が生む逆効果——人のせいにすることで隠れる本当の問題とは?
今日の申し送り
人間はミスをする生き物。いい加減に気づけ!ばかたれリーダー共!
工場で働いていると、こんな言葉をよく耳にする。
✅ 「ミスをするやつが悪い」
✅ 「気をつけていれば防げるはず」
✅ 「ノーミスは当然」
確かに、作業ミスが発生すると、生産ラインが止まり、品質問題が発生し、会社にとって大きな損失になる。その責任を作業者に押し付けることで、管理者は楽になるし、改善コストもかからない。だが、本当にそれでいいのか?
実は、「ミスは作業者の責任」として処理し続けた結果、逆にコストが増大し、生産性が低下している工場が多いのだ。特に、日本は「ノーミス文化」が根強く、欧米の工場と比べて管理の仕方が大きく異なる。
この記事では、日本のノーミス文化がもたらす問題点を掘り下げ、海外の工場との違いを比較しながら、本当に効果的なミス対策とは何かを考えていく。
ノーミス文化が生み出す負の連鎖
日本の工場では、ミスを作業者の「注意不足」「能力不足」として処理する傾向が強い。しかし、その結果、現場では以下のような問題が発生している。
① ミスの隠蔽が発生する
「ミスを報告すると怒られる」環境では、作業者が小さなミスを隠すようになる。これが積み重なると、後で大問題に発展する。
例えば
食品工場では小さな異物混入を報告しにくい雰囲気があると、品質クレームが増え、最終的に大規模リコールにつながるリスクが高まるなど。
② 作業スピードが低下する
「絶対にミスをするな」と言われると、作業員は慎重になりすぎてしまう。その結果、生産性が落ち、現場の効率が悪化する。
③ ミスの根本原因が放置される
ミスを作業者のせいにすると、
✅ 設備の問題
✅ マニュアルの不備
✅ チェック体制の甘さ
といった本当の原因が改善されないまま放置される。その結果、同じミスが繰り返される。
海外の工場との比較:日本はなぜ「人のせい」にしがちなのか?
日本の工場と海外の工場を比較すると、ミスに対する考え方に大きな違いがある。
日本 | アメリカ | ドイツ | |
---|---|---|---|
ミスの扱い方 | 作業者の責任 | プロセスの問題 | 技術と仕組みの問題 |
ミス報告の文化 | 叱責・罰則が多い | 改善のための分析重視 | ミスが起きにくい設計 |
管理者の姿勢 | 「気をつけろ」で済ませる | なぜ起きたかを調査 | 設備や仕組みを強化 |
① アメリカ:「プロセスが悪いからミスが出る」
アメリカでは、ミスを個人の責任ではなくシステムの欠陥として捉える。
テスラやボーイングの製造現場では、ミスが発生すると「作業者を責める」のではなく、「どこにシステムの穴があったか?」を分析する。
例:アメリカの工場での対策
✅ 作業員がミスをしたら、「なぜそのミスが起こったのか?」を5回掘り下げる(ホワイ・ファイブ)
✅ 設備やマニュアルに問題があれば、改善策を考える
② ドイツ:「ミスが起こる前に技術で防ぐ」
ドイツでは、そもそも人間がミスをしないように「技術でカバーする」文化がある。
BMWやメルセデス・ベンツの工場では、AIやロボットを積極的に導入し、人間の判断ミスを減らす仕組みが整えられている。
例:ドイツの工場での対策
✅ 人が手作業でやる部分を極力減らし、自動化を進める
✅ ミスが発生するポイントにセンサーを設置し、リアルタイムで監視
このように、日本の「ノーミス文化」は、海外と比べると「人間の努力」に依存しているのが特徴だ。しかし、それは本当に効果的なのか?
なぜ「人のせい」にすると失敗するのか?
① 責任転嫁すると、問題の本質が見えなくなる
ミスの原因を作業者の注意不足にすると、設備や工程の問題が見落とされ、何度も同じミスが繰り返される。
② 作業者のモチベーションが低下する
「ミス=罰則」の環境では、作業者は新しいことに挑戦しづらくなる。結果、現場の成長が止まり、技術力が低下する。
③ 長期的に見るとコストが増大する
短期的には管理者が楽かもしれないが、長期的に見ると…
✅ 同じミスが繰り返され、品質トラブルが増える
✅ 作業者が辞めていき、新人教育コストが増える
✅ 隠蔽体質が生まれ、大きな事故につながる
では、どうすればこの問題を解決できるのか?中編では、ノーミス文化が生まれた背景を掘り下げ、本当に効果的なミス対策を考えていく。
ノーミス文化が生まれた理由と海外との違い
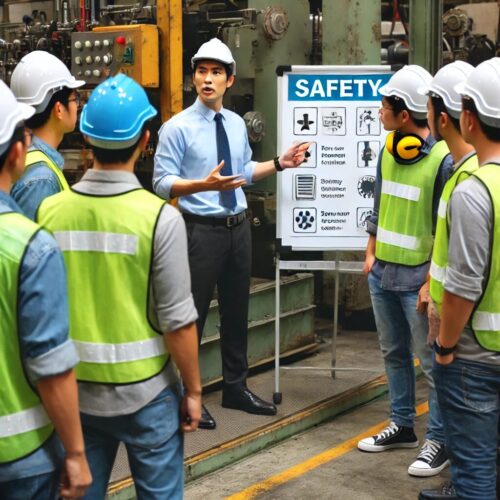
もともと日本は「ミスを作業者のせいにする文化」ではなかった
現在、日本の工場では「ミスをしたら作業者の責任」という考え方が根付いている。しかし、かつての日本では、ミスを「個人の失敗」として処理するのではなく、**「チームで解決する」**文化があった。
① 職人文化:「ミスは学びの一環」
昔の職人の世界では、ミスを繰り返しながら技術を身につけるのが当たり前だった。徒弟制度では若手が失敗することを前提に、師匠や先輩がフォローしながら育てる文化があった。
② 高度経済成長期:「現場主義とチームプレー」
戦後の工場では、現場の作業員同士が協力し、生産性を向上させることが重視されていた。ミスが発生しても、「どうすれば再発を防げるか?」というチームでの議論が主流だった。
しかし、日本が「ミス=個人の責任」とする文化へ変わっていったのには、いくつかの歴史的背景がある。
③ なぜ「ミスを作業者のせいにする文化」が生まれたのか?
- トヨタ生産方式(TPS)と品質管理の強化
- 1950年代以降、日本の製造業は品質管理を徹底し、「ミスをゼロにする」文化を推進。
- しかし、それが極端に進み、「ミス=作業者の責任」という意識が強まった。
- バブル崩壊後のコスト削減圧力
- 1990年代以降、企業がコスト削減を最優先し、人員削減が進む。
- ミスの責任を個人に押し付けることで、組織全体の負担を減らそうとする動きが強まった。
- グローバル競争による「責任の明確化」
- 2000年代以降、欧米型の「責任の明確化」を取り入れ、ミスが発生した際の責任が個人に集中する傾向が強まった。
このように、「ミスは作業者の責任」という考え方は、日本の伝統文化ではなく、近代の経済的・管理的な理由で生まれたものだ。つまり、この文化は変えることが可能であり、
「仕組みでミスを防ぐ」考え方に戻ることが、今後の日本の製造業にとって重要
だと言える。
ノーミス文化が根付いた背景
① 戦後の品質管理と「カイゼン」
日本の製造業は戦後、世界トップレベルの品質を誇るようになった。その中心にあったのが「トヨタ生産方式(TPS)」や「カイゼン(改善)」だ。
- 不良品を減らし、無駄を省く
- 人的ミスを極限まで減らす
- 厳格なチェック体制を構築
これらの考え方が、日本の工場に「ノーミス文化」を根付かせた。しかし、これが極端に進むと、「ミス=個人の責任」とする考え方が強まり、作業員へのプレッシャーが増大した。
② 日本の「責任文化」とヒューマンエラー
日本では、「組織のミス」を「個人の失敗」として扱う傾向が強い。たとえば、
- 工場でミスが発生すると、作業者が責められる
- 管理者は自分の責任を回避するために、作業者の意識の問題として処理する
- システムや環境の問題が見過ごされる
この結果、「ノーミスを維持するための管理」ではなく、「ミスをした人間を叱責する文化」が形成されてしまった。
③ 長時間労働と疲労の影響
日本の労働環境は長時間労働が常態化している。
- 疲労がたまることでミスが発生しやすくなる
- しかし、ミスを作業者のせいにするため、労働環境は改善されない
- 結果として、同じミスが繰り返される
このように、日本では「人間の頑張り」に依存するノーミス文化が根付いている。一方、海外の工場はどうなのか?
2. 海外の工場との比較
① アメリカ:「プロセスが悪いからミスが出る」
アメリカでは、ミスを「個人の責任」ではなく「システムの問題」として捉える。たとえば、
- ホワイ・ファイブ(5 Whys):ミスが発生すると、「なぜ?」を5回繰り返して根本原因を特定する
- エラーを許容し、学習の機会とする
- プロセスを見直し、改善する文化がある
例:航空機メーカーのボーイングでは、パイロットの操作ミスが発生した場合、単にパイロットを責めるのではなく、「なぜその操作ミスが起こったのか?」を徹底的に分析し、システム改善に活かしている。
② ドイツ:「ミスを防ぐのは技術と仕組み」
ドイツでは、「人間はミスをするもの」という前提で、技術や仕組みを整えている。
- 作業者に依存せず、システムでミスを防ぐ
- AIやロボットを活用し、判断ミスを減らす
- 作業効率を上げるため、適切な休憩や労働環境の整備を重視
例:BMWやメルセデス・ベンツの工場では、人間のミスを減らすために、センサーやAIを活用して作業の正確性を保っている。
③ 日本と海外の比較まとめ
日本 | アメリカ | ドイツ | |
---|---|---|---|
ミスの扱い方 | 作業者の責任 | プロセスの問題 | 技術と仕組みの問題 |
報告のしやすさ | 叱責・罰則が多い | 改善のための分析重視 | ミスが起きにくい設計 |
管理者の姿勢 | 「気をつけろ」で済ませる | なぜ起きたかを調査 | 設備や仕組みを強化 |
日本の工場は、「人が頑張ること」に依存しているのに対し、アメリカやドイツは「仕組みでミスを防ぐ」ことに注力している。この違いが、結果として生産性や職場のストレスレベルにも影響を与えている。
日本のノーミス文化の問題点を整理
日本のノーミス文化は、一見すると合理的だが、実は以下のような問題を生んでいる。
① 責任転嫁により、根本的な改善が進まない
- ミスを作業者のせいにするため、プロセスや設備の問題が放置される
- 結果的に、同じミスが繰り返される
② 作業員のストレスが増大し、離職率が上がる
- 「ミス=罰則」の職場では、作業者が疲弊し、モチベーションが低下
- ベテランが辞め、新人が定着しないことで教育コストが増加
③ 長期的に見てコストが増加する
- ミスを隠す文化ができると、大事故や品質問題につながる
- 繰り返し発生するミスによる生産ロスが増大
- 教育コストや採用コストがかさむ
中編 まとめ
✅ 日本は「人が頑張ること」に依存しすぎている
✅ アメリカは「プロセスを改善」、ドイツは「技術で防ぐ」
✅ 「人のせい」にすることで、むしろコストが増える
では、どうすれば日本の工場でも「ミスを減らしつつ、管理者の負担を減らせる」のか?
後編では、
✅ 日本の現場で実践できる改善策
✅ 「人のせいにしない」職場づくりの方法
✅ 実際の企業の成功事例
を紹介していく。
ミスを減らしつつ、管理者の負担を減らす方法
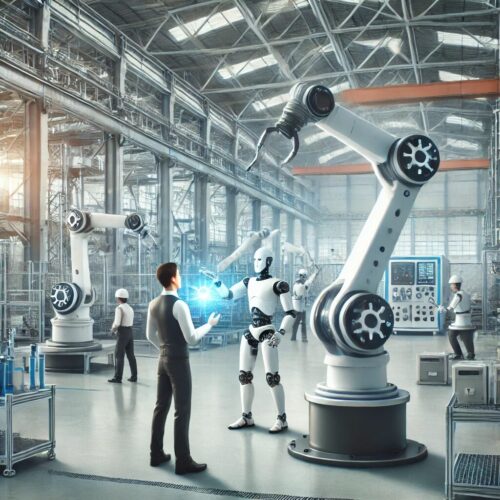
前編・中編では、日本の工場が「ノーミス社会」に陥りがちな背景と、海外との違いを掘り下げた。では、どうすればミスを減らしながら、作業者への過度なプレッシャーをなくし、管理者の負担も軽減できるのか?
後編では、具体的な解決策と実際の企業の成功事例を紹介していく。
ミスを減らすための「人に頼らない」仕組み作り
日本の工場では、「気をつけろ」「もっと注意しろ」といった精神論がまだまだ根強い。しかし、それでは根本的な解決にならない。ミスを本当に減らすには、「人の努力」ではなく、「仕組み」を作ることが重要だ。
① ヒューマンエラーを前提とした設計をする
✅ ポカヨケ(ミス防止策)を導入
- 例:自動車工場では、部品の向きを間違えないように専用のガイドを設置
- 例:ネジの締め忘れを防ぐために、トルクセンサーを取り入れる
✅ チェックリストや標準作業手順(SOP)の見直し
- 例:医療現場では、手術前後のチェックリストを厳格に運用し、ミスを防ぐ
- 例:工場でも、工程ごとに「確認ポイント」を明確化することで人的ミスを減らす
② ミスを責めるのではなく、仕組みを改善する文化を作る
✅ ミスが起きたら、原因を「5 Whys」で掘り下げる
- 「なぜこのミスが起こったのか?」を5回繰り返し、真の原因を特定する
- 例:「作業者が部品を間違えた」→「なぜ?」→「部品の置き場が分かりづらかった」→「なぜ?」→「ラベルの色分けが統一されていなかった」
✅ ミスを報告しやすい環境を整える(心理的安全性の確保)
- ミスを隠蔽する文化ではなく、「ミスは改善のチャンス」と考える
- Google社の研究でも、「心理的安全性が高いチームほど生産性が向上する」と示されている
③ IT技術やAIを活用してミスを減らす
✅ AIによるエラーチェックの導入
- 例:AIカメラを使い、製品の不良や作業手順ミスを自動検出
- 例:機械学習を活用し、過去のデータからミスが起こりやすいポイントを予測
✅ RPA(ロボティック・プロセス・オートメーション)の活用
- 例:単純作業を自動化し、人間がミスをしやすい工程を減らす
- 例:製造業では、品質検査をAIと機械に任せ、人的エラーを排除
✅ デジタルツインの活用
- 例:実際の生産ラインをデジタル上に再現し、シミュレーションを行うことで、問題が発生する前に対策を打つ
実践例・成功事例
では、実際に「ノーミス文化」から脱却し、ミスを減らすことに成功した企業の事例を紹介しよう。
① トヨタ:ポカヨケの徹底でヒューマンエラーを防ぐ
トヨタ生産方式(TPS)では、「ポカヨケ(ミス防止策)」を徹底している。
- 作業工程ごとにポカヨケ装置を設置
- 例:組み立てラインでは、間違った部品がセットされると警報が鳴る仕組みを導入
- 異常が起きたらラインを止める「アンドン」システム
- ミスをその場で修正し、未然に問題を防ぐ
- 「なぜなぜ分析」で根本原因を特定し、二度と起こらないようにする
この仕組みにより、トヨタは「作業者の努力」ではなく、「仕組み」でノーミスを実現している。
② ドイツ・BMW:AIと自動化でミスを削減
BMWの工場では、AIと自動化を積極的に活用している。
- AIカメラで部品の取り付けミスをリアルタイム検出
- ロボットアームが精密な作業を行い、人間のミスを削減
- デジタルツインを活用し、設計段階からエラーを防ぐ
このように、「人間が気をつける」のではなく、「技術でミスを防ぐ」ことに重点を置いている。
③ アメリカ・航空業界:「ヒヤリハット報告」を徹底
アメリカの航空業界では、ヒヤリハット(ニアミス)を積極的に報告する文化がある。
- ミスを責めるのではなく、再発防止策を考える
- 「危なかったけど問題は起こらなかった事例」も共有し、未然に防ぐ
- これにより、安全性が向上し、事故率が低下
この仕組みは、日本の製造業にも応用できる。ミスを隠さず、積極的に共有することで、事故を未然に防ぐことができる。
後編のまとめ
✅ 「気をつけろ」ではなく、「仕組み」でミスを防ぐ
✅ ポカヨケ・AI・RPAを活用し、人間の負担を減らす
✅ ミスを責めず、「改善のチャンス」と捉える文化を作る
日本の工場も、「人のせい」にするだけではなく、技術と仕組みでミスを減らす方向へシフトするべきだ。そうすれば、作業者の負担も減り、管理者の手間も少なくなり、結果的に生産性も向上する。
これからの時代、ノーミス社会から脱却し、**「仕組みでミスをなくす工場」**を目指していこう。
まとめ
日本の工場では「ノーミス文化」が根強く、作業者のミスを個人の責任として処理する傾向がある。しかし、その結果、ミスが隠蔽されたり、作業効率が低下したりと、むしろ現場に悪影響を与えている。本記事では、日本のノーミス文化の問題点を明らかにし、海外の工場との違いを比較しながら、より実践的なミス防止策を提案する。
🔹 記事の要点まとめ
✅ 前編:ノーミス文化の実態と問題点
- ミスを作業者のせいにすると…
- ミスが隠蔽され、後で大きな事故につながる
- 作業スピードが落ち、生産効率が悪化する
- 根本原因が改善されず、同じミスが繰り返される
- 海外との比較(アメリカ・ドイツ)
- アメリカ:ミスは「プロセスの問題」と捉え、分析・改善を重視
- ドイツ:AIや自動化技術を活用し、そもそもミスが起こらない設計
✅ 中編:ノーミス文化が生まれた背景と課題
・もともと日本は「ミスを作業者のせいにする文化」ではなかった
- 職人文化:「ミスは学びの一環」
- 高度経済成長期:「現場主義とチームプレー」
- なぜ日本は「人のせい」にしがちなのか?
- 戦後の品質管理文化(トヨタ生産方式・カイゼン)が強すぎる
- 「責任文化」により、個人の意識や注意に依存しすぎる
- 長時間労働が常態化し、疲労によるミスが増えている
- 海外との違いを再確認
- 日本:作業者の注意力に頼る
- アメリカ:ミスを分析し、プロセスを改善
- ドイツ:技術・システムでヒューマンエラーを防ぐ
✅ 後編:ミスを減らしつつ、管理者の負担も減らす方法
- 「気をつけろ」ではなく、「仕組み」でミスを防ぐ
- ポカヨケ(ミス防止策)の導入(トヨタのアンドンシステムなど)
- AI・RPAの活用(BMWのリアルタイムエラーチェックなど)
- ヒヤリハット報告の促進(航空業界の安全管理)
- 成功事例
- トヨタ:ポカヨケとアンドンシステムで人的ミスを激減
- BMW:AIと自動化により、ミス発生率を低下
- 航空業界(アメリカ):ヒヤリハット報告により、安全性向上
🔹 結論:ノーミス社会からの脱却へ
✅ ミスは「人のせい」にするのではなく、「仕組み」で減らす
✅ 海外の工場のように、プロセス改善や技術導入を進めるべき
✅ 心理的安全性を確保し、ミスを共有・学習する文化を作る
これからの日本の工場は、「作業者の頑張り」に頼るのではなく、「ミスを防ぐ仕組み」を作ることで、持続可能な生産体制を築くべきだ。
人間はミスをする生き物。これは絶対なのだ。いい加減気づいて、ミスを責めるのではなく仕組みを疑う文化を早急に構築する。でないと日本の製造業に明るい未来はもうやってこないかもしれない。